3D printing turns a digital design into a solid three-dimensional physical object by adding layer after layer of material. The process varies by technology, from desktop printers that melt plastic to industrial machines that use lasers to fuse metal powder.
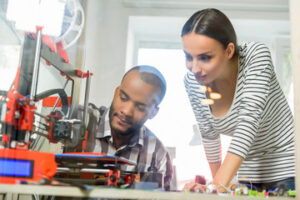
3D printing (or additive manufacturing) is the process of turning a digital model into a solid physical object by building up layers of material. This differs from traditional manufacturing processes that work by cutting away material (a subtractive process). Visit Our Website for more information.
3D printed objects can be made of a wide range of materials, from PLA plastic used for toys and food containers to titanium surgical implants. The technology is often employed in prototyping and research, but it has also become a valuable tool for businesses that are looking to shorten the product development cycle or create custom products.
The process starts with a digital model that can be designed using a 3D design software program like TinkerCad, which is available on the Windows computers in the OTS labs, or from a pre-existing model downloaded from one of many online repositories. The file is then imported into a software program that’slices’ the model into thin layers. Each slice is an instruction to the printer on how to build up a particular part of the object.
Slicing software also calculates factors like print time, layer height and infill density to determine how long the printed object will last and the best settings for it’s strength. The sliced model is then sent to the 3D printer, which builds up each layer of the object until it is finished. Depending on the model, post-processing steps may be required to remove support structures and smooth the surface of the object.
All of the 3D printers in the OTS labs use the same basic printing method, but they vary by technology. Desktop printers use a filament-like material that is heated and melted by the print head to deposit onto a platform, creating each layer of the object. The melted plastic hardens as it cools. The machine then moves the print head and the platform in X and Y and Z directions respectively to deposit another layer of the object, which is then fused to the previous layer.
Other methods, such as direct metal laser sintering (DMLS) and directed energy deposition (DED), use powdered or wire metal source materials that are heatened by the printhead to form the desired object. The DED method is more precise, but it takes much longer to complete and produces less material than the other two processes.
Materials
3D printing uses a variety of plastics and resins to create physical models from virtual designs. Oftentimes, these prints are used to rapidly turn out prototypes during the design phase of new products. They can also be put to use during manufacturing as a means of creating finished, functional parts. Objects created using 3D printing range from plastic figurines and mold patterns to steel machine parts and titanium surgical implants.
The most popular 3D printers use a process called fused deposition modeling, or FDM, to create objects. This technique involves heating up filament and extruding it onto the print bed in layers. The heated filament bonds with the previous layer to form a solid, three-dimensional object.
There are several different types of 3D printer filament available, with each offering unique properties. PLA (Polylactic Acid) is the most common 3D printing material, offering high strength and excellent layer adhesion. It can be printed in a wide range of colors and has an attractive, smooth surface that accepts paint and super glue well for further customization.
ABS (Acrylonitrile Butadiene Styrene) is another popular option, known for its resistance to corrosive chemicals and physical impact. It requires a vented environment and has longer print times than PLA, but it produces a tougher, more durable finish.
Photopolymer resin is used for more advanced projects that require higher levels of detail and a more rigid structure. The resin is cured with UV light during the printing process, which helps to prevent warping or cracking once the print is finished. This type of printing is ideal for complex research prototypes and small figurines that need to retain detailed features.
Nylon is an extremely versatile material for 3D printing, with helpful qualities that make it useful in a broad array of applications. Nylon for 3D printing is available in several formulations, including PA6 and PA66, which are stiffer versions, and PA12, a flexible version. Nylon is a tough, durable plastic with good heat resistance and chemical resistance, making it an excellent choice for end-use components that will be exposed to harsh environments.
Designing for 3D Printing
The 3D printing process transforms a digital model into a solid physical object by adding layer upon layer of material. It is used to create tools and prototypes that would be too difficult or expensive to produce with traditional manufacturing methods. It is also used to make replacement parts for existing equipment and to create medical devices, such as dentures and splints.
The first step in designing for 3D printing is to begin with a clear concept in mind. Whether it is functional, like a tool or a prototyping part, or artistic, such as a sculpture or piece of jewelry, this will guide your design decisions. It is also helpful to sketch your idea on paper to help you visualize it and consider important factors, such as size, shape, and material.
Once you have a model in mind, you can use a variety of CAD software programs to make the necessary adjustments. These can include using smoothing settings to reduce rough edges, fixing overhangs by removing supports, and adding infill to increase strength. Additionally, slicing software can be used to convert the 3D model into a file that will be read by a 3D printer. This process can be time consuming and requires some experience to get right.
Once the model is ready, it can be printed on a variety of materials, including plastics and metals. Post-processing, such as sanding or polishing, may also be needed to achieve a desired finish. In addition, some models may require support structures to keep them stable while printing, which can be added in a number of ways.
It is also important to remember that the digital version of your design must contend with the laws of physics when it comes out of the printer’s nozzle. For example, a horizontal section that is not supported from below, such as a bridge, will sag and may need to be reinforced with supports. These can be added to the CAD model, or generated automatically by the slicing software and printed along with the part.
With a little practice, you will be able to use these processes to bring your creations from the computer screen into the real world. Once you have mastered the basics, it is fun to experiment with more advanced designs and materials.
Getting Started with 3D Printing
Unlike the kind of printing you’re more familiar with, which involves ink-on-paper, 3D printers use layers to create three-dimensional objects. During the process, a plastic polymer is heated and deposited in successive layers until the desired object has been completely built. This plastic is usually a type of polymer, like PLA (polylactic acid), PETG, or ABS (acrylonitrile butadiene styrene). Other materials such as metals can also be printed with some specialized industrial printers.
To create a print, you’ll need a digital 3D model and a slicer software program that can translate that model into instructions the printer can understand. There are several different programs that can do this, but the most user-friendly and affordable options are TinkerCAD or Cura. Using these programs, you can design your own models, or find ones online. Some popular sites to check out are Thingiverse and Shapeways.
Once you have your file and a suitable printer, the most important thing to remember is that 3D printing is an additive process, meaning that it builds up your object layer by layer until it’s complete. As a result, every print has its own unique challenges that you’ll learn from as you go along. If you don’t have experience with 3D printing, it’s best to start with something simple, such as a phone stand or keychain. These small experiments will help you get the hang of things, and will give you confidence before moving on to bigger projects.
In addition to learning how to print, it’s important to understand the post-processing that’s required for some prints. Depending on the material and your design, it may be necessary to smooth the surface of the printed object, paint it, or assemble multiple parts. It’s best to take your time when performing these tasks, as they can significantly affect the quality of your finished print.
We’re here to help you take your 3D print project from idea to physical object. Please submit your request well in advance of when you need your print completed, so that we can ensure someone is available to oversee the printing and that the printer will be working.