The type of American Plastic Molds used depends on the design of the plastic part. Molds with undercuts, threads and other complex features take longer to produce than simpler ones.
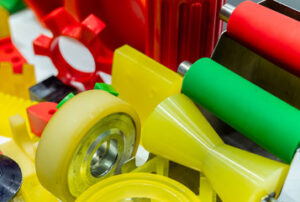
Injection molds have cavities and cores that shape the external and internal geometry of a part. Proper mold structure increases longevity. Slower cycle times also enhance mold durability.
Rotational moulding is a popular plastic molding process that uses hollow shapes to create high-quality polymer products. Its versatility and efficiency make it a popular choice in many industries, including automotive parts, food storage containers, toys, and water tanks. The steps for rotational moulding include accurately filling the mold, controlled cooling, and careful removal of the finished product. These steps ensure a strong and durable product.
First, the resin is pulverized to a fine powder. This powder is then loaded into a container or mould that is sealed shut. Then, it is rotated while heated to melt the polymer. Unlike injection or blow molding, which use an injector to force the polymer into the mould, rotomolding relies on gravity and centrifugal forces to draw the melted polymer into the hollow shape of the mould. Once the melted polymer is in place, the mold is cooled and allowed to harden.
The rotomolded product is then ready for use, and there is less waste than with other plastics manufacturing processes, such as injection or extrusion blow molding. Additionally, the rotomolded product can be decorated or branded with a wide variety of finishes. This process is ideal for creating consumer and medical products that need to be marked or branded with text, graphics, or other visual elements.
The most common materials for rotomolding are commodity based thermoplastics, such as low-density or high-density polyethylenes. This type of polymer is available in powder form, which simplifies the rotomolding process. In addition, polyethylenes offer good chemical resistance and low water absorption. However, a number of other materials are also being rotomolded, including polypropylenes and nylons.
One of the primary challenges with rotomolding is its long cycle times. Heating and cooling the large surface area of the mold takes time, especially when working with a thin wall material such as polyethylene. In addition, a significant portion of the polymer is exposed to the environment while rotating and heating, which causes degradation. This greatly limits the use of engineering plastics and reduces impact strength. The long cycle times also require that the molds be cleaned, inspected, and bolted shut between cycles, reducing productivity.
Extrusion Moulding
Plastic extrusion is a popular choice for manufacturing long linear products, such as pipes and tubes. The process is also well suited for creating thin sheets and films, such as those used in vinyl signs and window frames. It can be faster and more cost-effective than injection molding, especially for longer production runs. It can also be more efficient, since it produces less waste material in the form of sprues and runners — the channels through which molten plastic travels before entering the mold cavity. This efficiency aligns with sustainable manufacturing practices and reduces the environmental impact of production.
The first step in the extrusion moulding process is to mix base plastic material granules with any colorants, stabilizers, and additives that are desired. These additives can impart flame resistance, lubrication for easier shaping, or any other desired properties. This melted mixture is then fed through an extruder, which functions much like a giant blender, mixing and melting the plastic while keeping it homogenous. It’s then forced through a die, which shapes it into its final profile. The shape of the die determines whether you’ll end up with a pipe, a tube, or a piece of plastic film. Once the shaped plastic has cooled and solidified, it can be cut to length and finished as required.
Another advantage of the extrusion process is that it can be used with a wide range of polymer types, including both thermoplastics and thermosets. This allows manufacturers to select the best material for each specific project, ensuring the quality and strength of the final product. It’s important to note, however, that the type of plastic chosen will significantly affect the process’s speed and efficiency, as well as its overall effectiveness.
Continuous Moulding
Continuous moulding is a process in which liquid plastic is poured into a particular mold to harden and create the desired shape. This method of manufacturing is popular for creating products that require strength and durability. The liquid plastic is heated to high temperatures during the process so that it can maintain its shape and be trimmed afterward. It’s important to use the right tools and equipment to ensure that the process goes smoothly and effectively. There are many different types of molding processes available to manufacture your products, including injection moulding, extrusion forming, continuous injection, and cold stamping. Each one has its own advantages and disadvantages.
Injection moulding is a process that involves heating a polymer to above its melting point and injecting it into a mold. This type of moulding is ideal for producing large quantities of identical parts and complex geometries. The process can be used with a wide variety of materials, including thermoplastics and thermosets. The most common polymers for injection molding include PVC, PET, ABS, and PP.
SSI has experience with the injection molding of complex parts, such as gears, pumps, valves, and machine housings. This process requires a high degree of accuracy and precision, and can be difficult to master. However, with the proper techniques and expertise, injection molding can be a cost-effective and efficient way to produce large volumes of parts.
During continuous injection, inserts are held in a position within the mold cavity by a retractable core that is removed at some time during the injection process. The process aims to reduce the rejection rate of the final product, as well as increase production.
The molded metal, called a “strand,” exits the base of the mold and is cooled by a series of rollers. A group of rollers may also be used to bend the strand at an angle, such as 90 degrees. The strand is then cooled again to prevent oxidation.
There are several common defects that can occur during the continuous casting process. These include oscillation marks, surface cracks, and scarring. The causes of these defects are varied and may include improper cooling, lubrication, or problems with the mold.
Cold Stamping
Cold stamping is a type of metal processing technique that uses pressure to reshape sheet metal. It can be done at room temperature, and it can be used to create parts of various shapes and sizes. It can also be combined with other processes, such as hydroforming or extrusion, to create more complex products.
During the stamping process, a metal strip is pressed between two dies. The force applied to the dies can cause a separation or plastic deformation. The result is a part with a specific shape, size, and precision. This method is particularly effective for producing small to medium-sized components. It can also be used to decorate printed materials with metallic foils, a popular option for creating high-quality, eye-catching products.
In addition to providing an effective way to produce parts, cold stamping is also a cost-effective solution. Compared to other metal processing methods, cold stamping produces fewer waste materials and offers better dimensional accuracy. In addition, it can be performed as an inline process, reducing the number of steps in production. In addition, it allows manufacturers to create intricate designs and patterns that can be used for a variety of applications.
A wide range of industrial sectors use cold stamping to create a variety of products. This includes the automotive industry, machinery manufacturing, daily necessities, and electrical appliances. The process can be used to punch out parts in a wide variety of shapes, from the second hand on an instrument to car panel and longitudinal beams. Moreover, it can be used to make parts that are difficult or impossible to process using other methods.
The molds used for cold stamping can be made from different types of steel, depending on the product and the required manufacturing precision. In general, they need to have good toughness and fatigue fracture properties to prevent sudden brittle failure under operating conditions. Moreover, the molds must have adequate strength to withstand repeated stress loads and provide long service life.
During the cold stamping process, the metal is pushed through a series of rollers at room temperature. This process reduces the amount of heat needed to form the metal, and it also improves surface finish. The resulting product is stronger than hot rolled metal, and it can be cut to precise dimensions.